Service
Our company is engaged in all types of metalworking
- Home
- Service
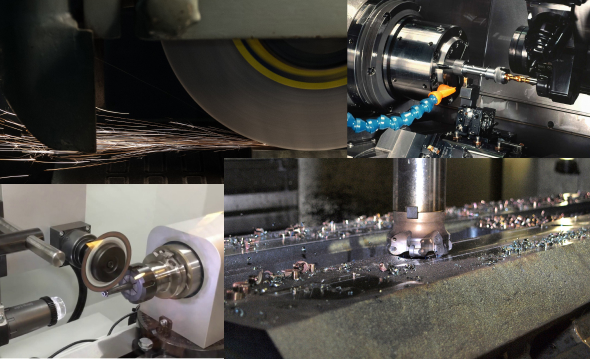
Grinding works
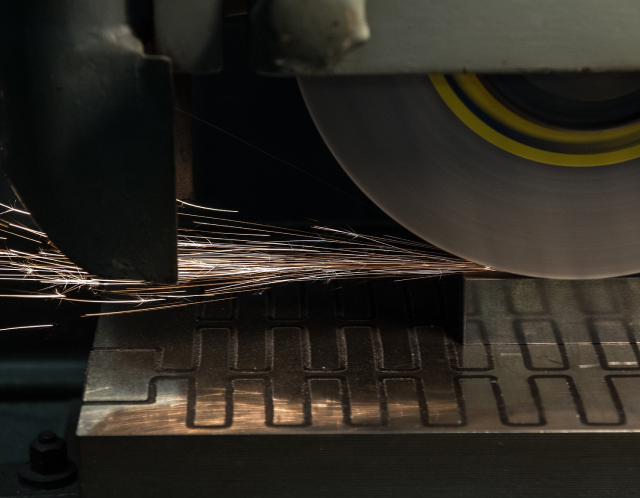
Grinding is the process of cutting metals using an abrasive
a tool whose cutting element is grains. Grains with high hardness and heat resistance
and sharp edges connected by special binders into grinding wheels, segments,
heads, bars and skins; grains are also used in the form of pastes and powders.
ur specialists in metal processing will perform the highest quality grinding work of various types on modern equipment.
ur specialists in metal processing will perform the highest quality grinding work of various types on modern equipment.
We perform:
- -flat grinding;
- -lat-carousel grinding;
- -circular external grinding;
- -round internal grinding.
Sharpening work
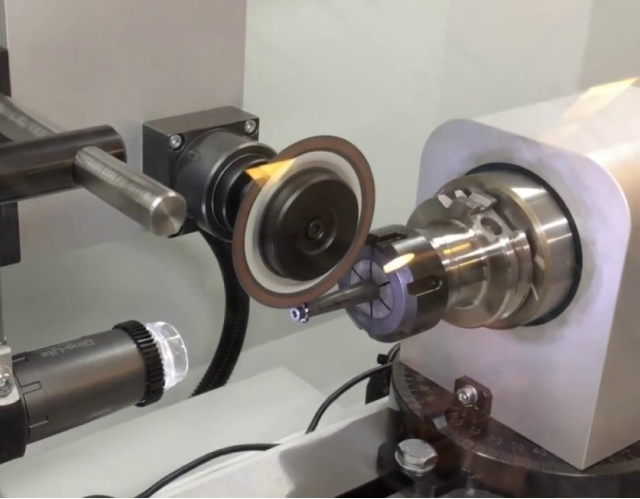
Keeping the cutting tool in working order
condition is provided by timely and high-quality sharpening - grinding of workers
tool surfaces.
The main purpose of the cutting tool sharpening process is as follows:
- - ensuring optimal geometric parameters of the cutting part of the tool, contributing to increasing its stability, as well as the accuracy and productivity of processing;
- - ensuring the specified roughness limits of the sharpened surfaces of the tool;
- - preservation and restoration of the cutting properties characteristic of the tool, with minimal permissible changes in its surface layers;
- - ensuring economic operation of the tool.
Milling work
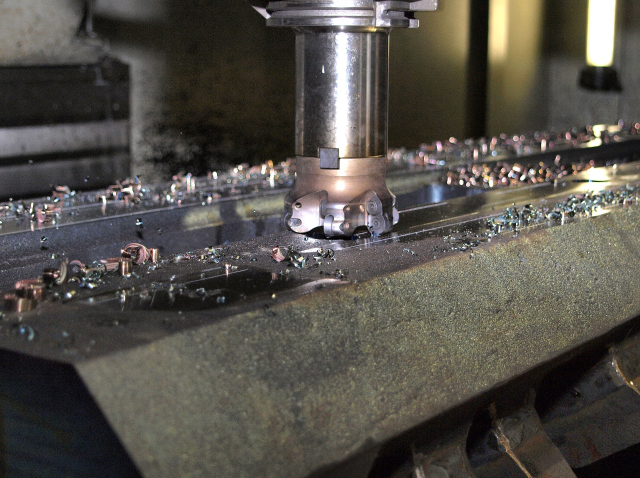
Milling operation in the manufacturing process
details is very important. Thanks to this operation, it is possible to make more accurate dimensions of some elements
details than when casting. The main tool for carrying out this operation is a cutter, hard
fixed on the shaft of the milling machine.
Due to the high revolutions of the cutter and the submission of the workpiece under at the right angle, direction and speed, the metal is removed from the workpiece quite easily, and most importantly from fairly high accuracy.
Due to the high revolutions of the cutter and the submission of the workpiece under at the right angle, direction and speed, the metal is removed from the workpiece quite easily, and most importantly from fairly high accuracy.
The main types of milling operations:
- -face milling (milling of large surfaces)
- -final milling (grooves, undercuts, grooves, pockets, wells, windows);
- -all types of milling are performed on modern CNC equipment.
Gear cutting work
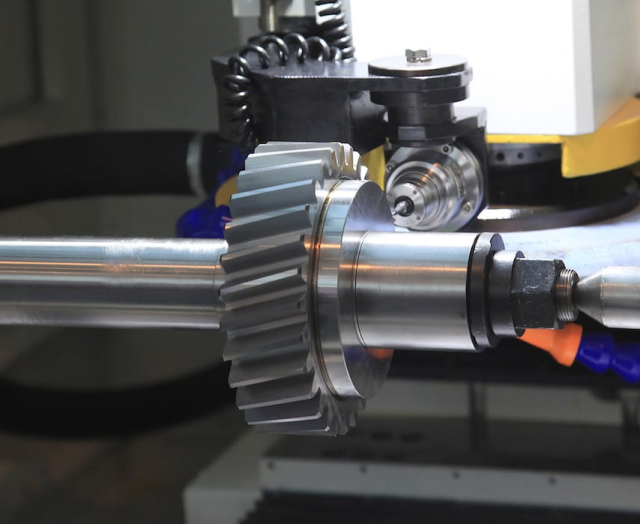
Gear cutting is a type of machining (machine machining).
The company will perform any type of gear cutting work: cutting gear wheels, cutting conical
gears, worm gears, incl. globoid coupling, splined joints, chevron coupling
other.
Our organization has a powerful enough tool section to perform gear cutting work according to the customer's drawings. Our workshop uses modular milling cutters and deburring tools for tooth cutting. Depending from the method of tooth cutting, modular disc or finger cutters and tooth-cutting heads are used for work by the copying method, tooth-cutting combs, worm cutters, chisels, tooth-cutting cutters and cutter heads for work by the break-in method.
The disk milling cutter is shaped and has a toothed tooth, the profile of which is radial plane corresponds to the profile of the depression of the toothed gear wheel.
Our organization has a powerful enough tool section to perform gear cutting work according to the customer's drawings. Our workshop uses modular milling cutters and deburring tools for tooth cutting. Depending from the method of tooth cutting, modular disc or finger cutters and tooth-cutting heads are used for work by the copying method, tooth-cutting combs, worm cutters, chisels, tooth-cutting cutters and cutter heads for work by the break-in method.
The disk milling cutter is shaped and has a toothed tooth, the profile of which is radial plane corresponds to the profile of the depression of the toothed gear wheel.
Turning work
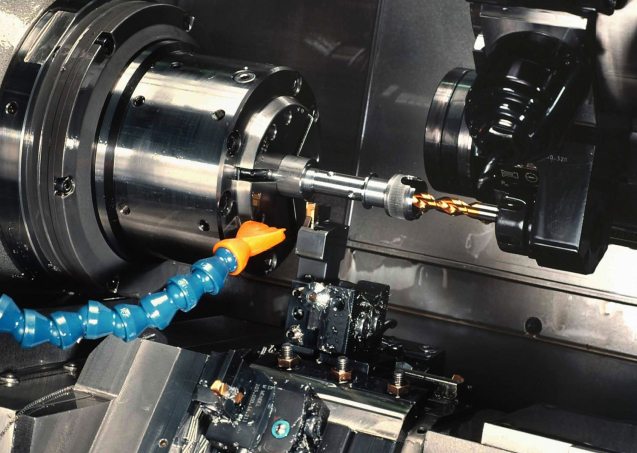
Turning is mechanical processing by cutting external and internal
surfaces of rotation, including cylindrical and conical, facing, cutting, chamfering,
processing of fillets, cutting grooves, cutting internal and external threads on lathes.
Types of turning:
- - turning - treatment of external surfaces;
- - boring - treatment of internal surfaces;
- - trimming - processing of flat end surfaces;
- - cutting - dividing the workpiece into parts or separating the finished part from the workpiece.
Rubberizing shafts
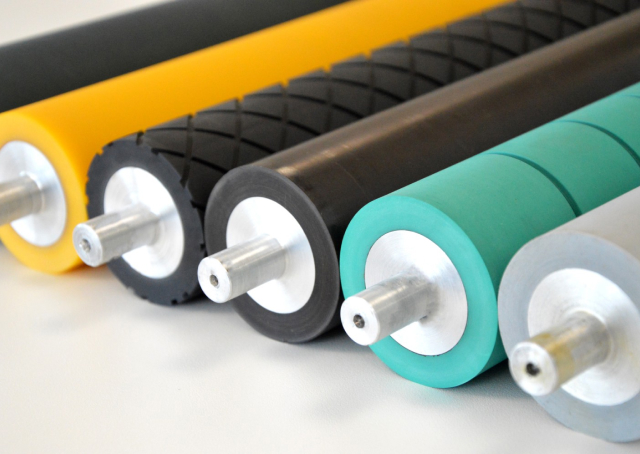
"Unirem" offers professional rubberization of shafts with high-quality raw materials.
In any production (and in almost any field) there are aggregates, proper work
which is impossible without rubberized metal parts. It can be shafts, rollers, drums and many more
what else The main purpose of rubber coating is to protect the metal surface from the destructive effects of the environment.
It is about both chemical mixtures and simple mechanical friction. Rubber is elastic, resistant to mechanical deformations In addition, the rubber coating reduces vibration, which allows you to reduce the noise level by almost a third. All together, this indicates one thing: the rubberization of the elements extends the service life of the entire structure and significantly increases the efficiency of its work.
It is about both chemical mixtures and simple mechanical friction. Rubber is elastic, resistant to mechanical deformations In addition, the rubber coating reduces vibration, which allows you to reduce the noise level by almost a third. All together, this indicates one thing: the rubberization of the elements extends the service life of the entire structure and significantly increases the efficiency of its work.
Our enterprise rubberizes metal using several technologies:
- - cold vulcanization;
- - hot vulcanization;
- - plates on bolts.